Quality Assurance

At HF, Fasteners are manufactured in 25000 Sq.ft built up area. This unit is an Integrated Manufacturing hub located in central part of Tamilnadu from wire rod to the final product screw.
We ensure the highest standards of quality .
We design and manufacture as per DIN 7504K German standard.
Systematic and Strict quality control procedures are followed.
Traceability:
Fasteners manufactured at HF are 100 % traceable using batch control process.
Due documentation are developed and a library of samples are maintained.
Quality Assurance Flow chart

Inspection Procedure
Mechanical Properties:
We at HF carry out a series of test to determine the mechanical parameters. Samples of 15 nos. are collected for every 10000-15000 screw pieces.
Following tests are carried out to confirm the quality parameters as per DIN standards
1. Torque strength - to determine the breaking threshold of the screws.
2. Surface and core hardness - studied using vickers hardness tester to study strength of screws.
3. Drilling Test - To determine the drilling time ensuring faster & stable drilling.
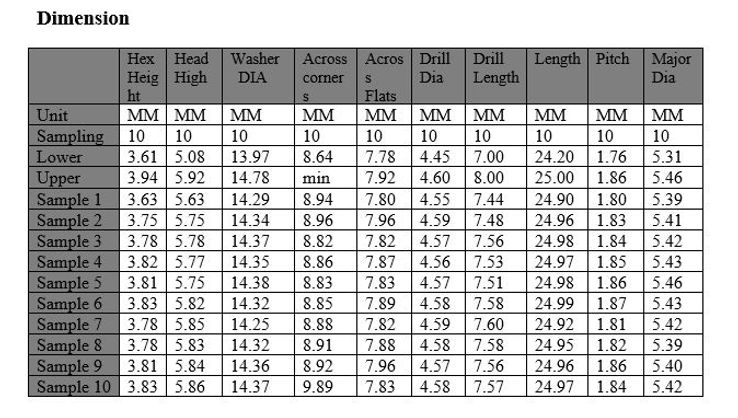
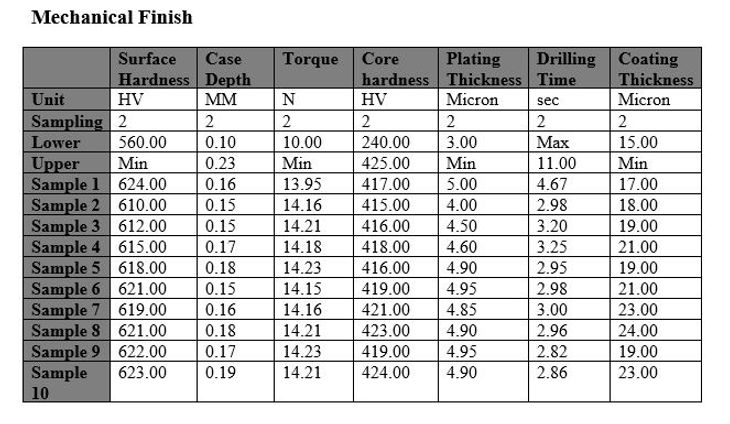
Surface Treatment
RUSPERT:
- Is a surface processing technology for providing anti-corrosion consists of three layers. 1st layer - mettalic Znic, 2nd layer - high grade anti corrosion chemical conversion film and 3rd layer of baked ceramic coating.
At HF, self drilling screws are surface treated in three anti- corrosive performance
1. Type 1: SST 500 hrs DIN 50018(0.2L) 15 cycles
2. Type 2: SST 1000 hrs DIN 50018(0.2L) 15 cycles
3. Type 3: SST 1500 hrs DIN 50018(0.2L) 15 cycles
Average coating thickness: 20 microns.
.